Can Gunmetal Scrap Be the Solution to World Hunger? Exploring the Innovative Humanium Metal Initiative
- yanabijoor
- Nov 3, 2024
- 2 min read
Problem
The problem is armed conflict and illegal firearms that contribute to poverty and world hunger in conflict areas.
Solution
The Humanium Metal initiative transforms seized illegal firearms and their gunmetal scrap into new metal. Companies buy this upcycled metal to make consumer products. The profits are reinvested into communities affected by gun violence to create a cycle of peace and development.
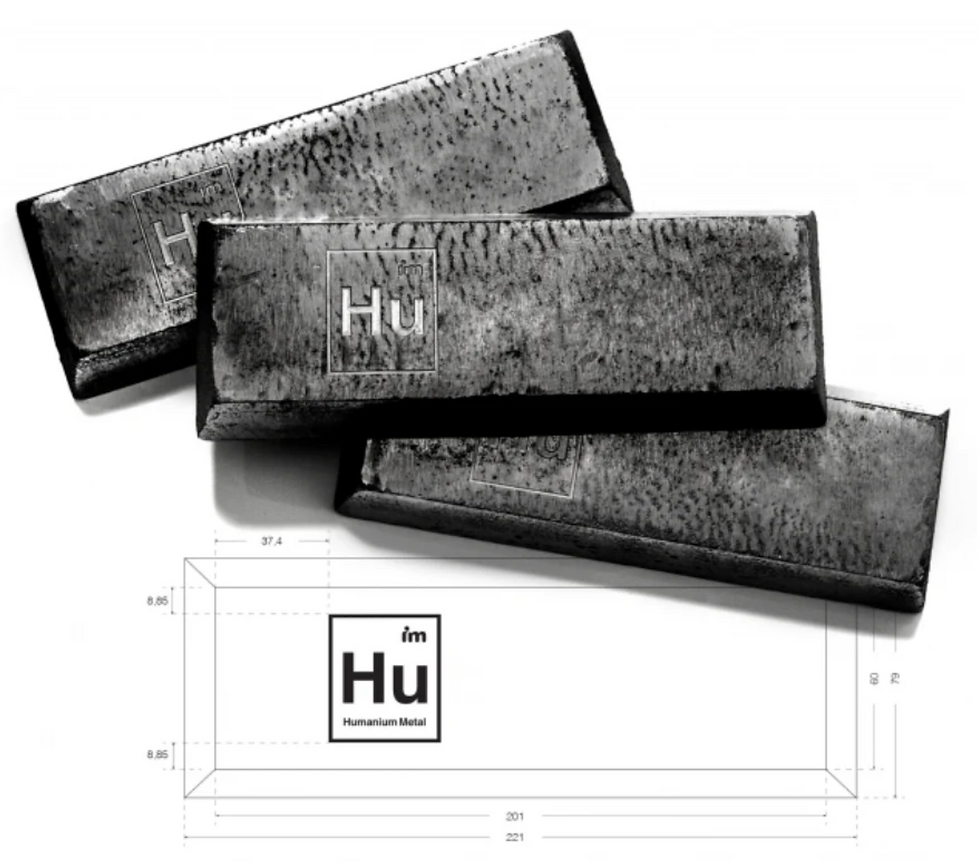
Why is this innovative?
This is innovative because upcycled materials are used for harm and converted into products for peace. By branding and transforming gun metal into a marketable precious metal, Humanium Metal raises global awareness about the harmful effects of gun violence. It is a clever way to unite governments, businesses, and civil society against gun violence.
What’s the impact?
Humanium Metal has destroyed around 12,000 illegal firearms and taken them out of circulation. The scrap has been used to make buttons and watches, and the proceeds have created new funding sources for violence prevention programs and survivors. The initiative has generated significant funds for these causes, such as the $150,000 Triwa Swisswatch Watchmaker donated to Individuell Människohjälp Swedish Development Partner (IM), a Swedish non-profit focused on initiatives helping those affected by gun violence.

What needs to be improved?
Turning gun metal into polished stainless steel has its challenges. First, you have to make a precise metal mixture, which has to be controlled to 18% chromium, 8-10% nickel, 2-3% molybdenum, and the rest iron. That requires monitoring and high precision to meet the quality standards.
Once the mixture is made, melting the metal mixture in a furnace at 3,000 degrees is energy-consuming and time-consuming. The liquid metal is then atomized by pouring it into a chamber and disrupting it with high-pressure nitrogen gas to form fine particles. This stage must be optimized for consistency and efficiency to produce uniform stainless steel powder.
The biggest challenge is transitioning to metal injection molding, as the stainless steel is in powder form. This process compresses the powder into solid form and takes almost a year and a half to perfect. Production time and cost can be reduced if this stage can be optimized.
Here’s how the process can be improved:
1. Precision and Efficiency in Mixing: Improve ways to monitor and achieve the precise metal composition to minimize waste and rework.
2. Energy and Time Efficiency: Look into alternative methods or technologies to reduce energy consumption and time for melting and atomization.
3. Optimize Atomization: Develop ways to get consistent and optimal particle size during atomization.
4. Simplify Injection Molding: Invest in R&D to reduce the lead time for metal injection molding so we can faster transition from powder to solid.
5. Quality Control: Implement quality control throughout the process to ensure the final material meets the standards.
Sources:
https://humanium-metal.com/products/’https://www.hodinkee.com/articles/would-you-wear-a-watch-made-from-a-gun
Comments